Darrington Quarries, which is part of leading resource management business FCC Environment, have been operating from their Cridling Stubbs site for over 60 years where they produce over 350,000 tons per annum of quality limestone, for use in a variety of independent ready mix concrete plants and to the local construction market.
Finedoor have recently designed, manufactured, and installed three new 5 mtr x 5 mtr x 200t tonne hopper bottoms. The original hopper bottoms had become badly corroded and with various repairs been undertaken over the years of services the decision was taken to have the bottom sections replaced prior to a major collapse.
Following the tender process, Finedoor was awarded the contract for the design, manufacture, and installation of the three new hopper bottoms with Darrington. The task of removing the old sections and the installation of the new sections, planning was key, with health and safety of the works been paramount. With the use of a mobile crane not being an option due to the roof, existing two screens and chutes in situ directly above the hoppers a telehandler proved to be the best.
The design was to be paramount, allowing for sectional pieces to be installed to complete a full hopper section and allow for bolting to the existing ring beam. Finedoor successfully completed the installation within our client’s timeframe, allowing for minimum disruption for the Darrington business.
Darrington Quarries general manager commented: ”The work was completed to a high standard, safely, on time and on budget,”
Mick Bray Finedoor’s engineering director commented, “The project was going to be challenging from the off, with the size and weight of the old hopper bottoms leaving us with limited options. We opted to remove the old bottoms as effectively and safely as possible, cutting and removing sections as large as possible in line with the telehandler and operators capacity. The design and manufacture of the new hopper section was critical, knowing our own employees had to be in situ when each panel was offer up, meant there would be no second chances. Given no access for a mobile crane and the scales of these hoppers, we always knew the project would be challenging from the start, but with excellent planning the project was delivered in a safe manner.“
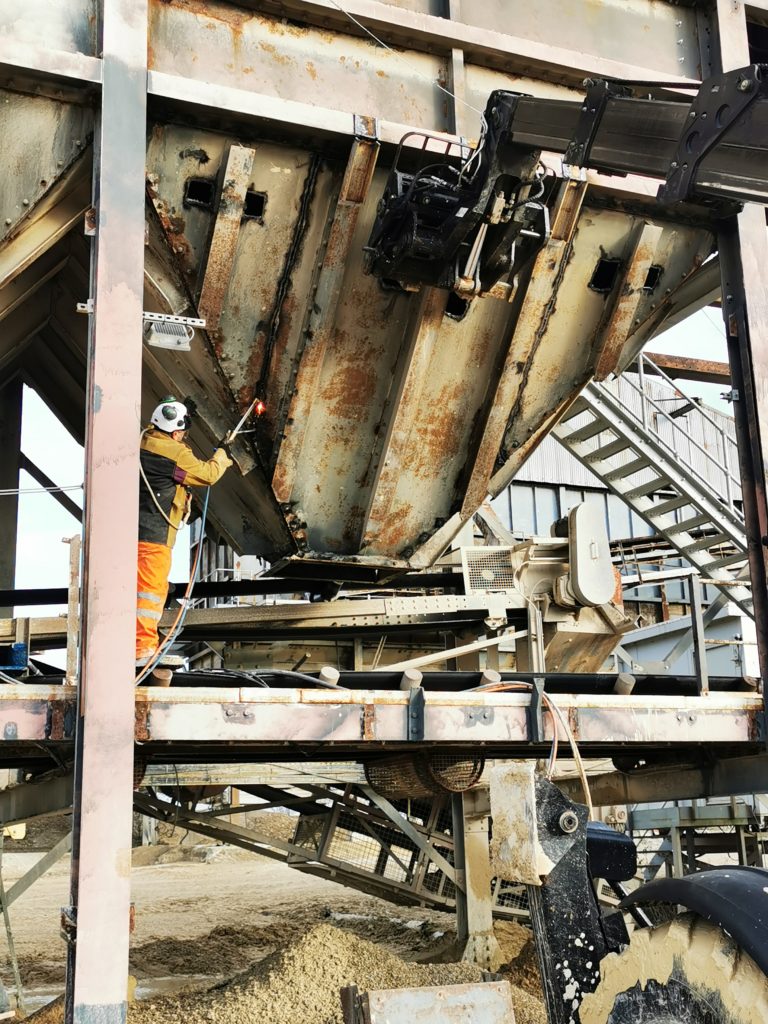
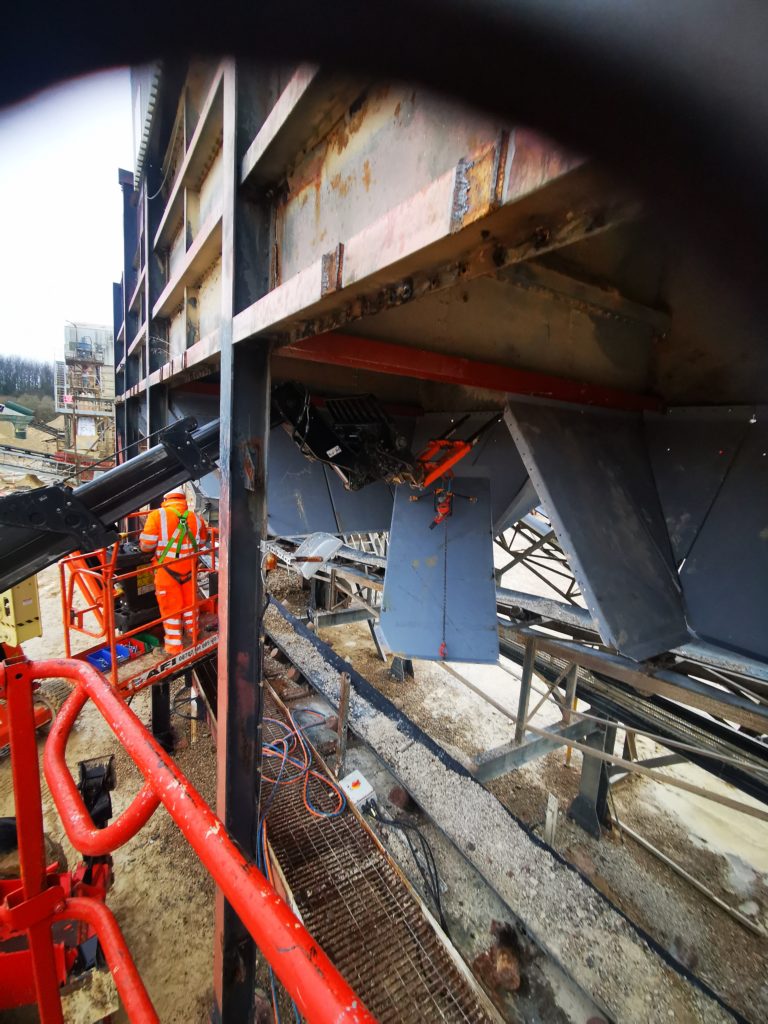
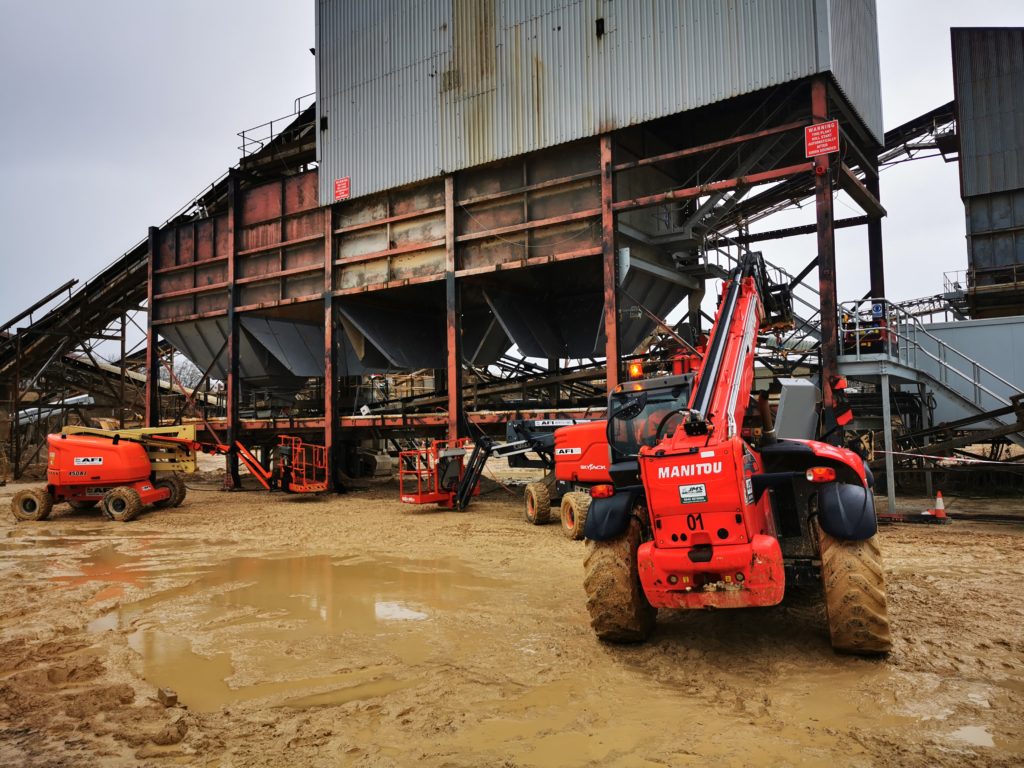
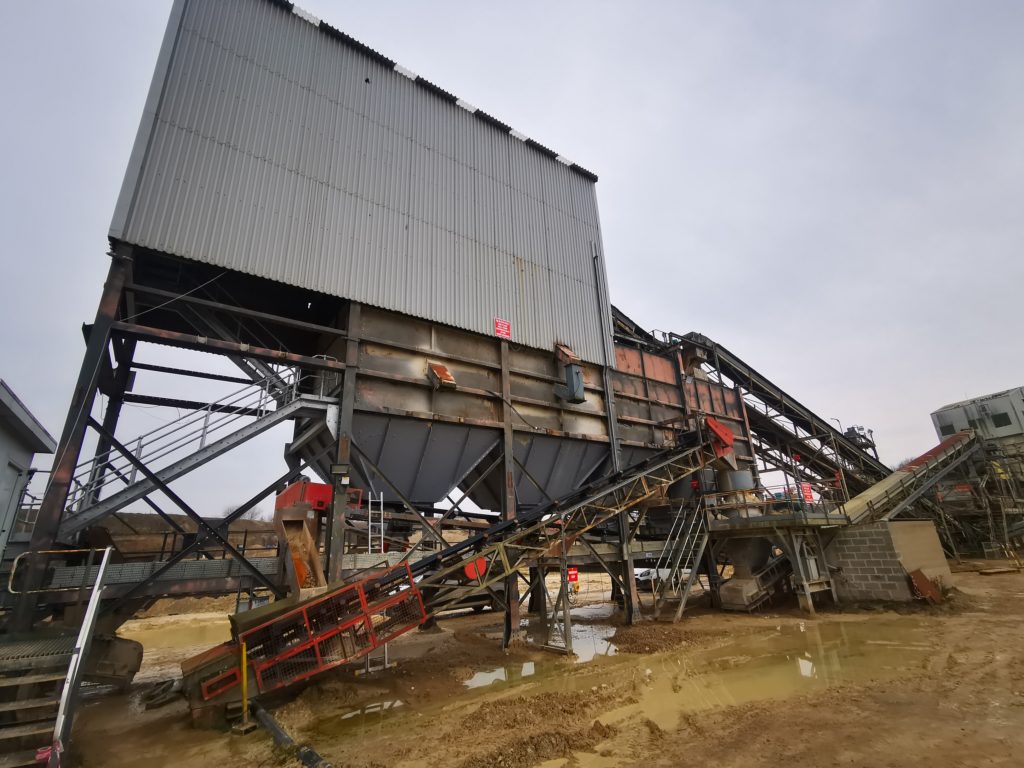